Since the 1970’s, the nuclear weapons industry has utilized the pulsed Nd:YAG laser welding process for joining of intricate/heat sensitive components. The characteristic high power density of the pulsed Nd:YAG laser welding process yields the lowest heat input fusion welding process available to the industry. In 1997, Precision Joining Technologies was founded at the Mound Facility in Miamisburg, Ohio and began using this unique process for the repair of molds used in the plastic injection mold industry.
This is accomplished by the addition/placement of filler material between the worn/damaged mold surface to be repaired and the laser beam. The laser beam melts the filler material with the mold steel yielding a built up surface which is slightly higher than the original part dimensions. Previous to the implementation of this process, other welding processes were used for mold repair which would cause distortion of critical dimensions on the mold and yield undercut(sink) of the mold base material next to the welded area.
The left photograph below shows the typical build up of a mold steel using filler wire. The left side shows the build up of the corner of the mold, the middle and right weld bead shows the top surface of the mold built up using a 0.010″ and 0.015″ diameter filler wire respectively. The right photograph is a cross-section of the corner weld.
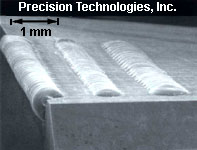
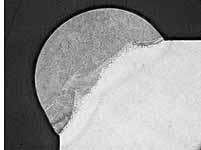
Used by permission. EMTEC‘s Mission is to improve industrial competitiveness by facilitating the development, deployment, and commercialization of materials and processing technology. EMTEC is Sponsored by the Ohio Department of Development. Precision Joining Technologies, Inc. is an EMTEC member.